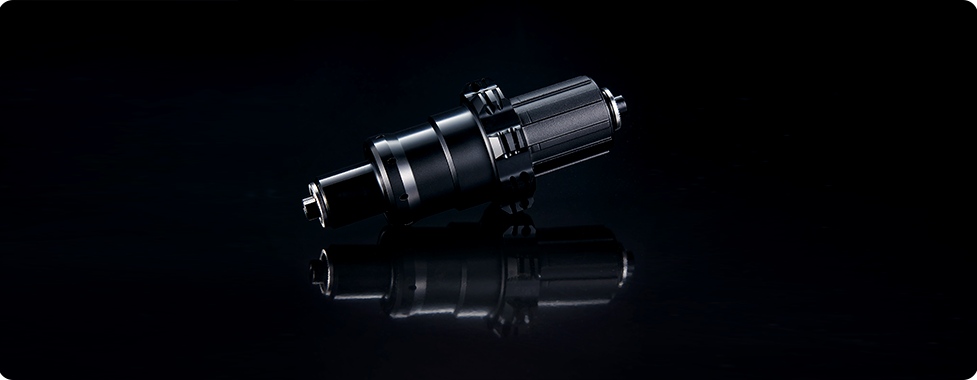
Consumer Products
Rear hub
This case concerns a bicycle wheel hub, one of the most fundamental components in a bicycle transmission system. This concept is unique from the traditional ratchet and pawl system and the star ratchet mechanism. With traditional ratchets like this, there are gaps between cogs so more rotations, or pedaling at a specific angle is required for it to engage and gain momentum. It is also possible to feel a delay when pedaling off the saddle. Our client’s hub was carefully designed to contain no gaps, so the energy exerted can be directly transmitted into motion. This offers the rider a more sensitive pedaling experience, increases performance, and lowers friction while coasting. This rear wheel hub belongs to the high-end market for bicycle parts.
In the preliminary evaluation stage, we took a closer look at the transmission design and configuration. We discovered the original placement of the internal bearing, as well as the constant movement that would have had an effect on the performance. We advised they make spatial adjustments. In addition, the original design used a tiny spring as part of the transmission mechanism. After further investigation by our team, we discovered that the use of these particular springs would increase the chance of defects, and due to the precision and quality they required during mass production, we advised that another spring be used. We also informed them that this would lead to a potential increase in costs. A plastic retainer, an alternative solution was considered to achieve the same result. The team then used 3D printing technology to manufacture the retainer. After testing the molding work, we discovered the mold had multiple microscopic holes or cutouts. Creating molds can be extremely difficult, but with the efforts of the HUBTICLE engineers, it merely took two weeks to develop the molds, complete the design, and prepare the evaluations for mass production.
Next, we entered the proofing stage, where we disassembled each part and produced all the samples simultaneously. We then reassembled them and adjusted the accuracy of each piece to save time on mold testing and optimization. The processing methods and optimization directions used for each part were vastly different. For the outer shell and ratchet seat (cassette body/freewheel body) sections, we used CNC milling and lathing machines and suggested further adjustments be done to the thickness of the body while maintaining its light-weight and durability. The appearance of the ratchet seat was obtained by analyzing the fringe projections and utilizing other reverse engineering techniques. Fortunately, the team experienced no further setbacks with the patent.

In the core parts, such as the processing of the retainer, as well as the inner and outer rings, it was much more of a challenge due to the high standards and manufacturing accuracy requirements needed for these parts. During the evaluation stage, the retainer still had multiple holes or cutouts and was very difficult to develop molds. Here we tried using a plastic injection process. It was also recommended that the client consider harsher climates to increase the lifespan of the product and special attention be given to the concentricity of the inner and outer rings to ensure a smoother rotation. This was done to avoid mechanism faults while extending the durability and lifespan of these parts. After the lathing process was actioned, it was sent to a heat-treatment processing plant to enhance the robustness and stability of the product. Furthermore, the internal and external diameters were also sent for precision grinding. The inner ring was subjected to wire electrical discharge machining (wire EDM), CNC lathing, CNC milling, heat treatment, and completed all the precision grinding processes.
We also noticed the internal bearing had five different forms, and the needle roller had varied sizes and dimensions. These all had to be analyzed, tested, and adjusted to achieve a balance between strength and durability while maintaining its light-weight. The grease is also very important as there are different types used according to specific characteristics. Other parts, like the axle, end caps, o-rings, and rubber dust cover cap were all adjusted to make it convenient for consumers to clean, assemble, and stay properly sealed. Upon completion, it was a much better-integrated design.
In addition to satisfying the client's design specifications, we also took the consumers’ needs for purchasing the product into account. The hub improvements that our team suggested not only facilitated easy cleaning and assembly but merely required a replacement retainer or needle roller over long-term use. This would reduce the need to replace the whole hub. After an adjustment was assessed by our team, the concentricity tolerance of the overall structure fell within 0.02 mm, which successfully reached the tolerance range set by the client.
This whole process was essential to make clear the numerous details that one needs to pay attention to when mass-producing goods and improving product yields. The samples were also delivered to a third party to test for strength and functionality. Within three months the product was manufactured from scratch and completed all SGS agency tests.
"I want to thank the HUBTICLE team for working so hard, day and night. You made it possible for us to display our products at the International Bike Exhibition."
Through mass production planning, HUBTICLE provides our clients with one-stop services from evaluation and proofing right through to large-scale mass production, where there is a no-minimum order restriction. This greatly reduces our customers’ inventory pressure, cost expenditure, and allow customers to focus more on marketing.
HUBTICLE is responsible for production, and we continue to grow and develop alongside our customers.